A Fresh Perspective on Quality Coding
16th February, 2018
The fresh produce sector remains buoyant. According to Euromonitor, fresh food continued to grow in both volume and value terms in 2016, reflecting the emergence of eating trends such as the consumption of organic and natural foods, and the general positive media coverage about fresh food. Indeed this focus on healthy eating has helped to change the UK’s eating habits over the years.
One example of the growth in fresh produce has been the success of soft fruits, where consumption in the UK has increased significantly over the past 20 years, with strawberries going up by 150% and raspberries 123% during this period, while the purchase of other types of soft fruit has risen by 316%. As a result, production of soft fruit in the UK has expanded by 131%. (Source: DEFRA)
Nevertheless, despite such successes, the fresh produce industry continues to face a number of challenges. Competitive markets inevitably put pressure on prices, meaning growers have to find ways to improve both productivity and efficiency. This is particularly vital given the manual nature of much of the work – and with only a tiny fraction of soft fruit production currently provided by UK nationals, the implications of Brexit may have a significant effect on both labour availability and wage costs.
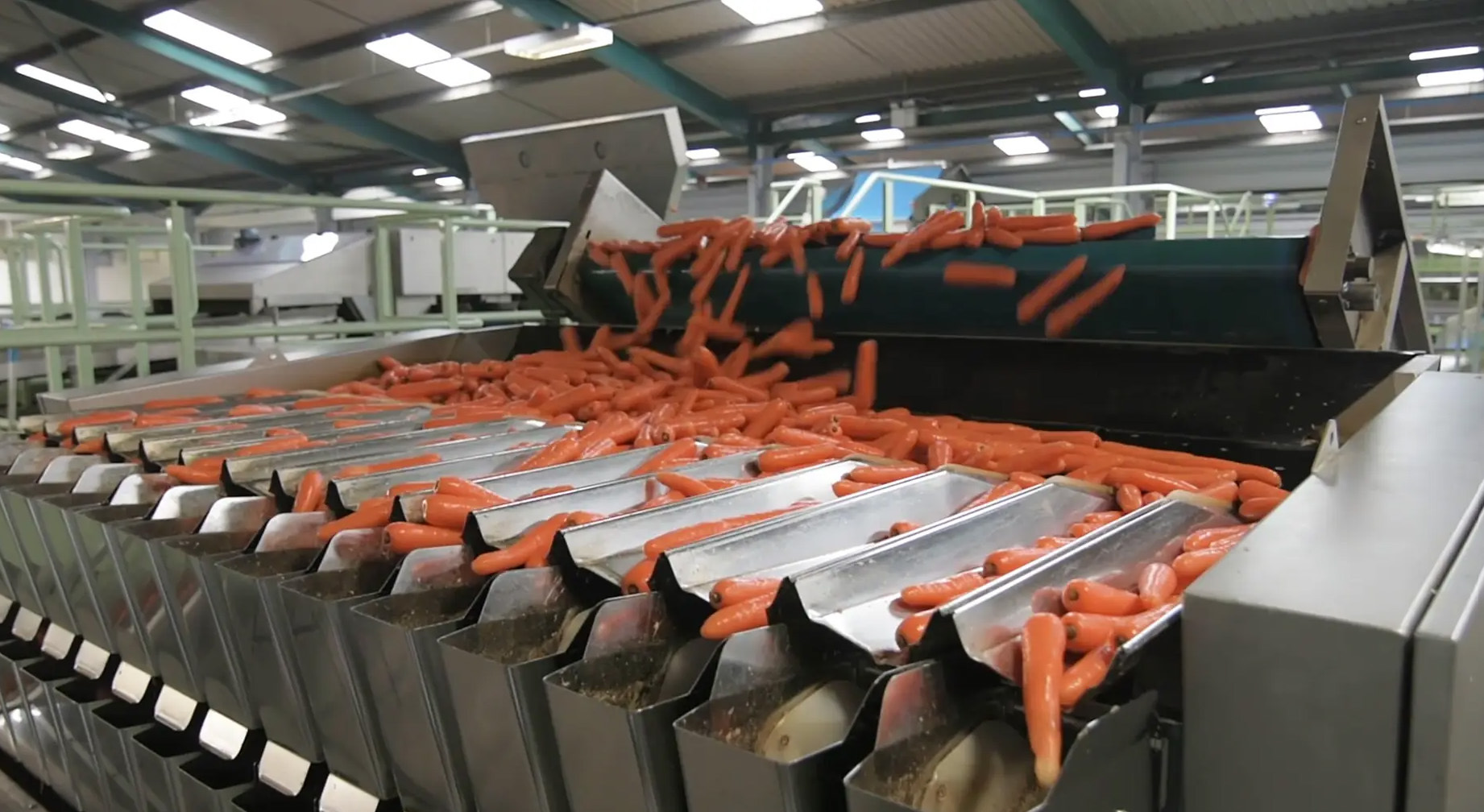
Efficient production is also essential for any type of fresh produce to ensure a fast and smooth process from picking to retail shelf, in order to deliver the longest possible shelf-life and highest quality to the end-consumer. Given the limited opportunity for repacking or reworking of product, errors must be avoided and a right-first-time approach adopted to minimise waste.
The selection of the right coding equipment plays a key role, particularly since no product can leave the factory without the appropriate printed information such as use-by dates or traceability data. Reliability is therefore critical, with key features to look for including machines with few moving or wear parts, such as clutches and brakes that require periodic replacement; longer intervals between servicing; and easier maintenance procedures including fast consumables changes and washdown designs that protect against dust and water ingress.
Achieving a high-quality print at the fastest speeds is equally important. One example of how this can be achieved is the ability of thermal transfer overprinters to print in both intermittent and continuous motion, enabling speeds to be matched to different production requirements. Another beneficial feature is self-maintaining printhead systems that automatically clean and re-prime the printhead before each print without slowing down the line.
Errors can be avoided with the use of simple touchscreen interfaces and on-screen help and prompts that make code creation more intuitive. Setup and editing authority can be limited for different users and the process can also be accessed and controlled remotely.
Another critical aspect of a successful and efficient operation is the quality of the code. To meet legislative and traceability requirements, as well as retailer standards, legibility is paramount. Equally true, a poor quality or smudged code can detract from the overall pack design and appearance, affecting brand image and consumer perceptions.
At the same time, research has shown that using more descriptive words for fresh produce can make it more enticing and increase consumption. The overall look of the packaging helps to support this, and coding equipment with the software to use different typefaces can ensure that the essential information contained in the code complements and does not detract from the overall look and appeal of the pack.
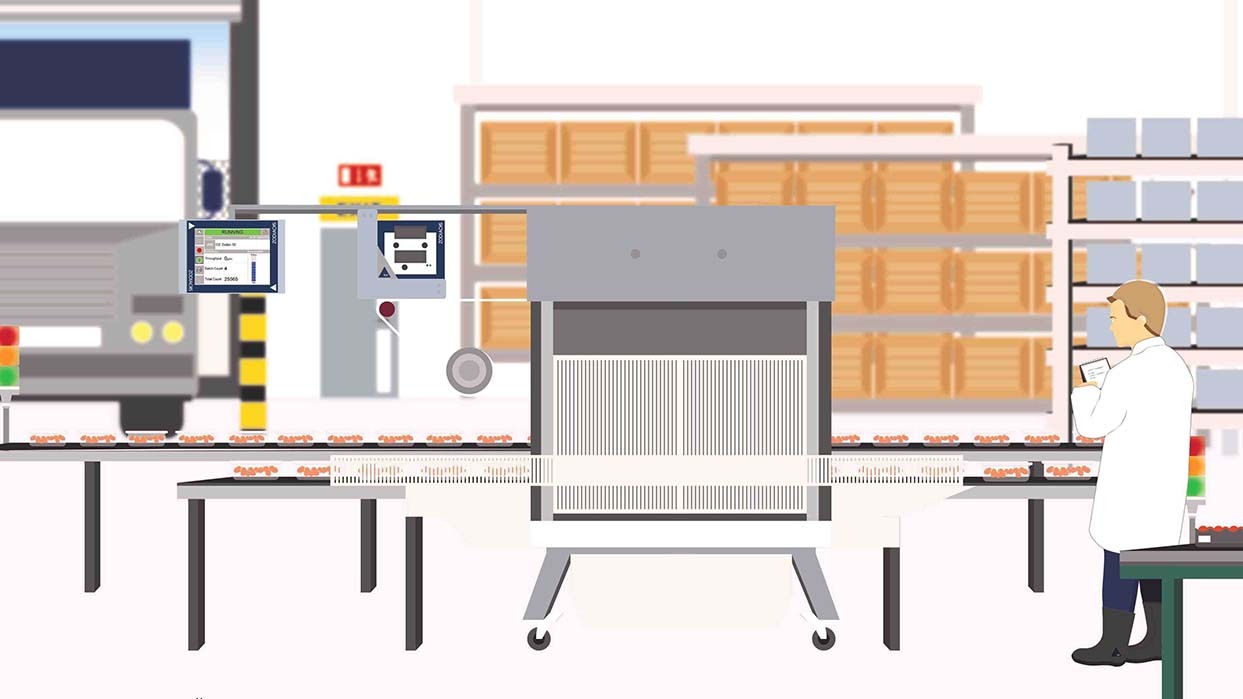
Monitoring of code quality is equally important. This avoids the cost implications of any recall but even if a problem is detected before the product leaves the factory, there are still major cost implications in terms of both product and packaging waste. In the past, such monitoring was carried out by a separate vision system on the line. However, defining the quality parameters for a code is not easy.
If they are too restrictive, many acceptable codes may be rejected, increasing waste and affecting efficiency. In addition, vision systems cannot always identify a gradual deterioration in code quality, which may mean some poor quality codes pass through undetected before packs start to be rejected.
This has led to the development of a new generation of coders that are now able to monitor and report on the quality of each code as it is produced. In our ICE Zodiac Hawk model, for example, internal checking system, iAssure™, assesses the spent ribbon after each code has been produced to determine whether the print quality is good enough. If the code is unacceptable, the machine signals for the pack to be rejected. If the fault persists, it can declare a trend of deterioration and stop the line entirely.
All information on poor quality codes, along with guidance for rectifying the problem, is reported on the control screen or can be accessed and printed off remotely. This provides the necessary early warning of any potential loss of code quality, enabling companies to take immediate actions and minimise downtime.
Disrupted production can play havoc with any fresh produce supplier’s profit margins. An effective coding system that delivers consistent high quality codes will enable businesses to save money, reduce waste and maintain and enhance brand reputation.
If you’re interested in improving Overall Equipment Effectiveness (OEE) by reporting on performance, reliability and quality, take a look at the ICE Zodiac Hawk or Get in touch on enquiries@uk.interactivecoding.com or give our team a call on 01159 640144.
Related
Brexit labelling changes for British produced foods sold into the EU
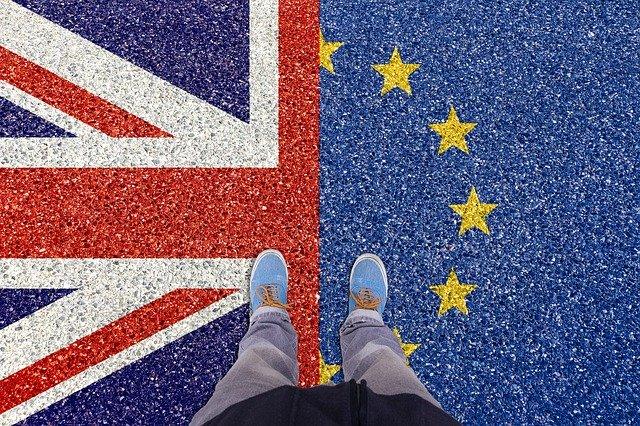